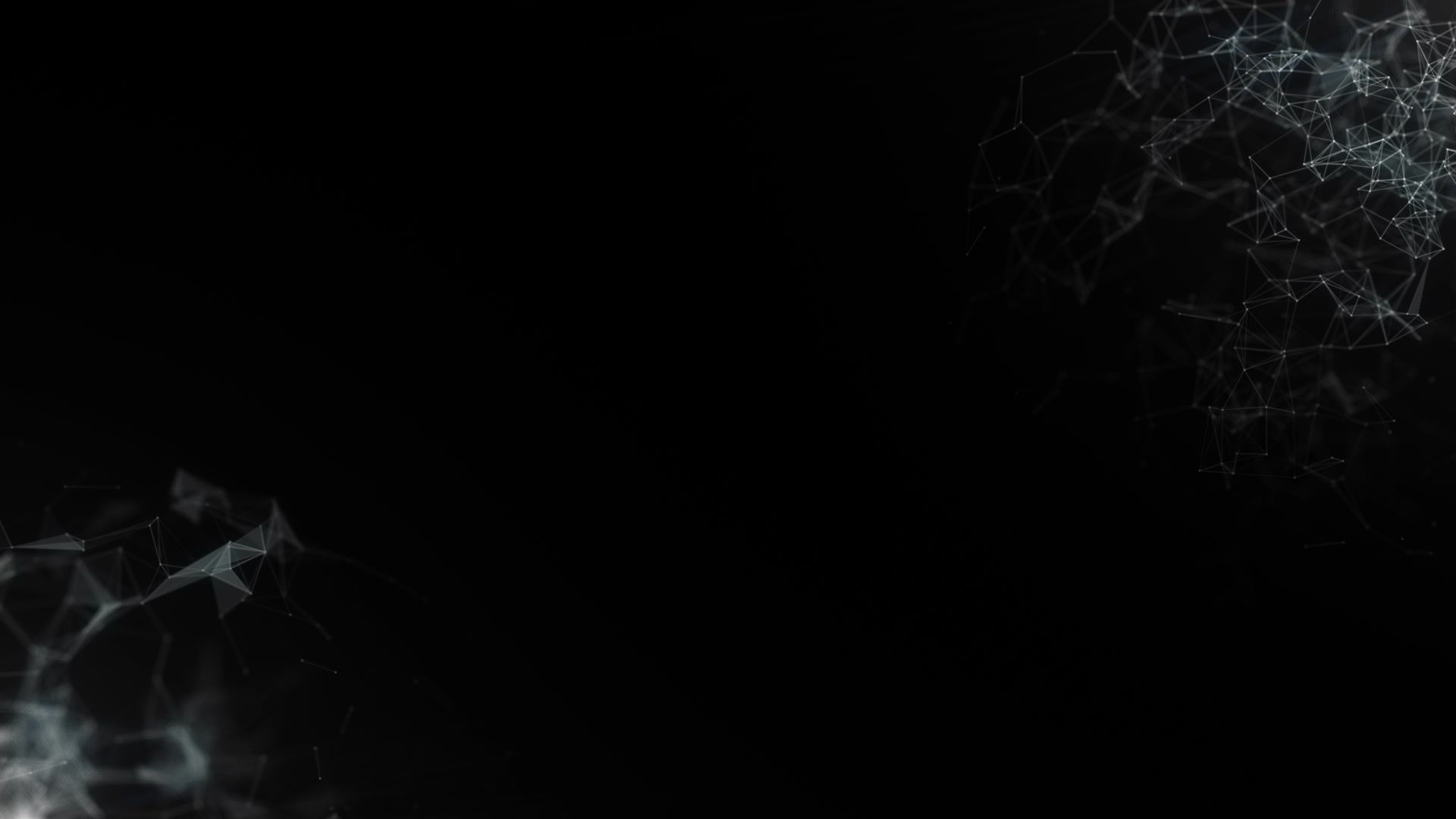
Laminados prensados con Vacío
El 11 de marzo de 2019, la Asociación Argentina de Aviación Experimental (AVEX), subió a YouTube, un video de una de sus charlas técnicas acerca de cómo realizar los contrachapados utilizando como prensa la fuerza del vacío. Román Lucas, quien estuvo a cargo de dicha charla, explicó con claridad cómo funciona este dispositivo y la forma de construirlo, detallando los elementos necesarios.
Esta charla dio sus frutos ya que varios constructores, con distintos proyectos, vieron las bondades de este sistema y ya se han realizado varios dispositivos.
Los terciados realizados por este método quedan muy parejos logrando un muy buen resultado.
Quería destacar que este sentimiento de compartir la información, instalado en la mayoría de los constructores de aeronaves experimentales, permite fortalecer esta actividad y generar un margen de seguridad al sumar las experiencias que cada uno va obteniendo.
En relación a mi proyecto, en principio he realizado los contrachapados, utilizando prensas con tornillos de distintas maneras. Este sistema funcionó bien en las medidas de ancho que he necesitado.
Posteriormente armé este dispositivo de vacío ya que en terciados más anchos facilita el prensado. Teniendo presente que cada constructor coloca su impronta en lo que realiza, voy a mostrar los distintos pasos de cómo lo he realizado. Espero que pueda ser de utilidad para quien quiera sumar esta herramienta de trabajo.
Este dispositivo consiste en confeccionar una bolsa, similar a una funda de almohada. Se requiere nylon transparente de 500 micrones de espesor En mi caso conseguí de 450 micrones y funcionó bien. El material requiere sellarse térmicamente, al no contar con la herramienta, el sellado fue realizado en un taller de lonas para camiones.
Las dimensiones están dadas de acuerdo a las medidas que van a tener los terciados a realizar. En mi caso las medidas de la bolsa son de 250 cm de largo por 100 cm de ancho. El lado que queda abierto es uno de los de 100 cm. Además esta bolsa requiere tener una perforación para conectar la manguera de vacío.
Dentro de la bolsa coloqué una madera de mdf de 9 mm de espesor, 90 cm de ancho por 230 cm de largo, que funciona como cama plana para las piezas a prensar. Es unos centímetros más chica que la bolsa para que entre con facilidad. A esta madera previamente le realicé varios canales en ambas caras para que circule con facilidad el vacío, estos canales convergen en el lugar de la toma de la manguera de vacío. En los cruces de los canales perforé orificios para que se conecten, entre sí, las dos caras de la madera. Coloqué la toma de vacío del lado de abajo de la madera para que me permitiera deslizar el material con facilidad y aprovechar al máximo el tamaño de esta madera.
Esta distribución de vacío se logra de muchas maneras, con telas , tejido de cerco plástico etc...

Canales realizados con un tupí. Los canales fueron cubiertos con cinta plástica a fin de suavizar los bordes y también para que no se marque la bolsa de la cama.
Toma de vacío
Contorno redondeado. Es muy importante redondear y lijar las aristas ya que se ejerce mucha presión y el material plástico se puede romper.
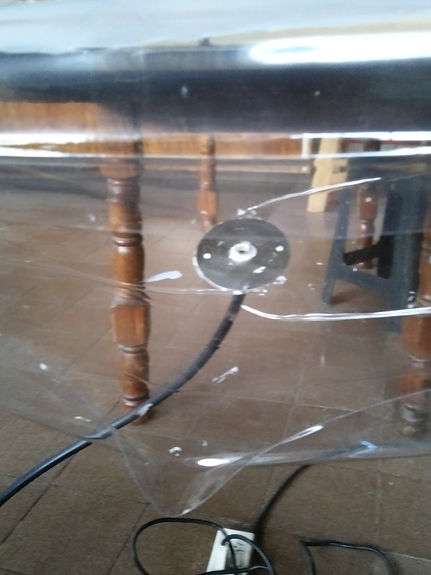
Realicé la toma de la manguera de vacío colocando dos arandelas de vuelo ancho, una de cada lado del nylon, pasé un caño roscado, coloqué una tuerca de un lado y del otro, un tetón para manguera, fijando con sellador las arandelas y apreté el conjunto.

Vista de abajo con el vacío ejerciendo presión .
En la madera realicé un hueco para permitir que entre el caño roscado con tuerca y además sirve como apoyo para la arandela. De esta manera la tensión del plástico es pareja.
Acá se puede apreciar la manguera con su abrazadera apoyada sobre la madera, absorbiendo parte de la presión.
Para cerrar la parte abierta, se pliegan los bordes plásticos de la abertura y se aprietan con prensas, con dos listones de madera ,hierro, aluminio, etc. La finalidad es que el vacío no se pierda, no requiere mucha presión.
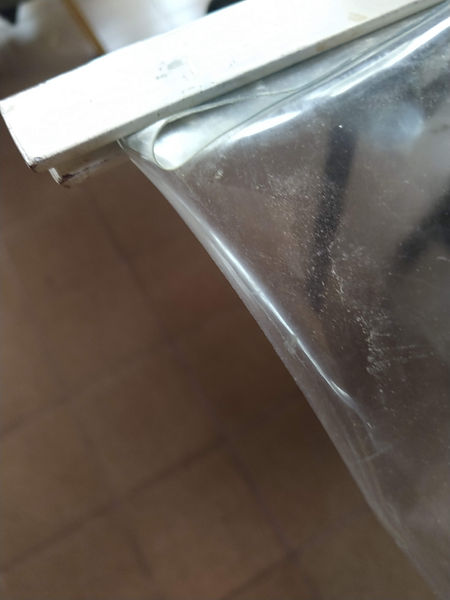


Acá podemos ver como queda el sellado térmico
Para generar vacío utilicé el motor de un nebulizador. Es habitual el uso de un motor de heladera, conocido como bocha.
Una vez que logramos generar vacío en la bolsa, utilizando una bomba de vacío, necesitamos controlarlo para que sea estable durante el tiempo que requiere el fraguado del adhesivo (24 hs. aproximadamente).
Para esto se utiliza un instrumento, conocido comercialmente como vacuestato, cuya función es abrir o cerrar un circuito eléctrico, en función del cambio de un valor de vacío prefijado.
Vacuestato Casero
Para controlar y mantener estable el vacío, uno de mis hijos realizó este dispositivo con tecnología de Arduino.
Posee un display para poder identificar y seleccionar a qué presión enciende el equipo o lo apaga, esta selección la realizamos nosotros, a través de botones de comando. Cuenta con un sensor atmosférico dentro de la manguera de vacío, que identifica la presión atmosférica, dentro del sistema. Esta información es enviada al procesador.
El procesador da la orden a un relay de acuerdo a los parámetros elegidos de corte o encendido, esto incide en la toma eléctrica del motor.
En la cañería coloqué un reloj analógico de vacío para poder cotejar el sistema electrónico con uno mecánico. Cuenta con una llave que permite el encendido directo del motor con el objetivo de que si falla la parte electrónica podamos mantener el sistema encendido.
Enchufe para el motor
Encendido sistema electrónico

Encendido directo del motor
Display
La manguera de vacío llega hasta la caja para facilitar el conexionado. En este lugar se encuentra el sensor atmosférico
Botones para programar el dispositivo

Válvula de retención de vacio adicional.
Tuve que colocarla porque la válvula que trae el nebulizador no retenía el vacío y lo iba perdiendo lentamente.

Centralicé los diferentes elementos del dispositivo en una madera para facilitar su desplazamiento.
Alimentación del sistema de 220v.
El reloj esta cm Hg .
Luego de experimentar con diferentes configuraciones decidí que lo mejor, en este caso, era que el sistema corte a -42cmHg y vuelva a activarse cuando la presión llegue a -35cmHg.
Dicha configuración permite que el sistema se mantenga en una presión adecuada para el pegado; sin que llegue a niveles demasiado bajos y permitiendo una rápida recuperación de la misma.
Al realizar terciados planos, el sistema tarda aproximadamente 40 segundos en llegar al nivel de vacío previamente elegido. En cambio, cuando se trata de terciados curvos, debido a las bolsas de aire que se forman al utilizar el molde para el plegado del mismo, el sistema tarda significativamente mas tiempo en lograr el vacío inicial.


Vista del conjunto

El telgopor que está debajo del reloj es para que no vibre mientras funciona el motor.
Con una TEE derivé hacia el reloj y el sensor atmosférico
Algunos laminados realizados en la cama de vacío


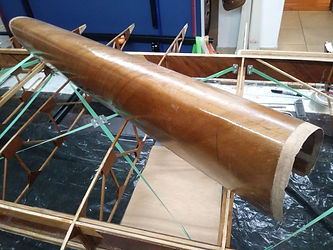
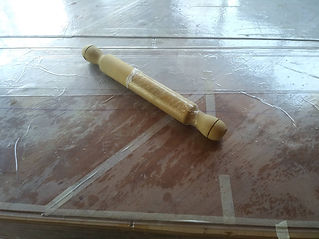
Al inicio, cuando el vacío comienza a ejercer presión, aparecen burbujas de aire y pliegues, que podemos ayudar a desplazar, utilizando, por ejemplo, un palo de amasar (si no es ofrecido gentilmente, comprar uno...)